While we try to keep things accurate, this content is part of an ongoing experiment and may not always be reliable.
Please double-check important details — we’re not responsible for how the information is used.
Automotive and Transportation
Soft Wire Act: Revolutionary Robot Can Carry Cargo Up and Down Steep Aerial Wires
Researchers have created a light-powered soft robot that can carry loads through the air along established tracks, similar to cable cars or aerial trams. The soft robot operates autonomously, can climb slopes at angles of up to 80 degrees, and can carry loads up to 12 times its weight.
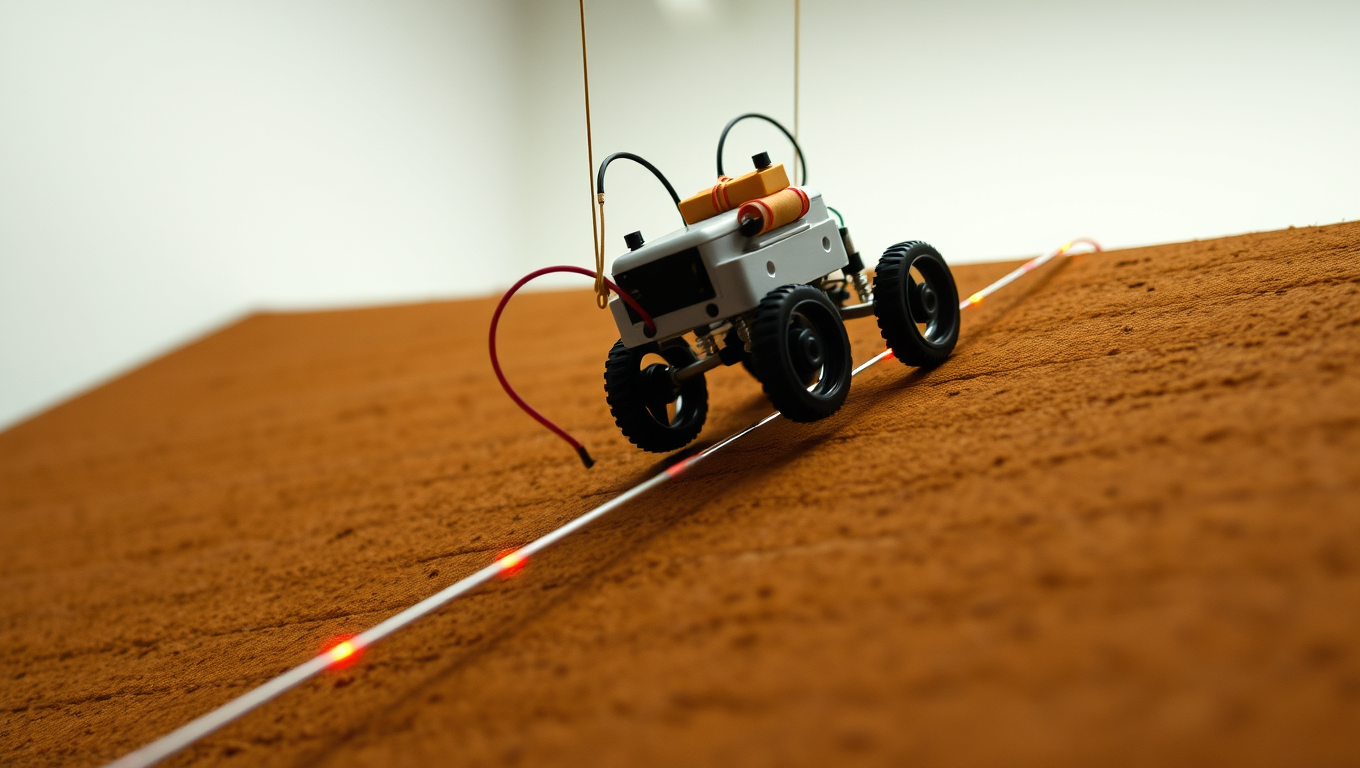
Automotive and Transportation
“Revolutionizing Battery Life: Scientists Uncover Secret to Making Aqueous Batteries Last 10x Longer”
A team at KAUST has revealed that the short lifespan of aqueous batteries is primarily due to “free water” molecules triggering harmful chemical reactions at the anode. By adding affordable sulfate salts like zinc sulfate, they significantly reduced this issue—boosting battery life over tenfold. The sulfate acts as a “water glue,” stabilizing the water structure and halting the energy-wasting reactions. Not only is this solution simple and cost-effective, but early results suggest it may be a universal fix for various types of metal-anode aqueous batteries.
Automotive and Transportation
A Breakthrough in Ammonia Production: Harnessing Human-Made Lightning for Sustainable Fertilizers
Australian scientists have discovered a method to produce ammonia—an essential component in fertilizers—using only air and electricity. By mimicking lightning and channeling that energy through a small device, they’ve bypassed the traditional, fossil fuel-heavy method that’s been used for over a century. This breakthrough could lead to cleaner, cheaper fertilizer and even help power the future, offering a potential alternative fuel source for industries like shipping.
Automotive and Transportation
Breakthrough in Green Hydrogen Production: Triple-Layer Catalyst Supercharges Energy Yield by 800%
Researchers in Sweden have developed a powerful new material that dramatically boosts the ability to create hydrogen fuel from water using sunlight, making the process eight times more effective than before. This breakthrough could be key to fueling heavy transport like ships and planes with clean, renewable energy.
-
Detectors4 months ago
A New Horizon for Vision: How Gold Nanoparticles May Restore People’s Sight
-
Earth & Climate5 months ago
Retiring Abroad Can Be Lonely Business
-
Cancer5 months ago
Revolutionizing Quantum Communication: Direct Connections Between Multiple Processors
-
Agriculture and Food5 months ago
“A Sustainable Solution: Researchers Create Hybrid Cheese with 25% Pea Protein”
-
Chemistry5 months ago
“Unveiling Hidden Patterns: A New Twist on Interference Phenomena”
-
Albert Einstein5 months ago
Harnessing Water Waves: A Breakthrough in Controlling Floating Objects
-
Diseases and Conditions5 months ago
Reducing Falls Among Elderly Women with Polypharmacy through Exercise Intervention
-
Earth & Climate5 months ago
Household Electricity Three Times More Expensive Than Upcoming ‘Eco-Friendly’ Aviation E-Fuels, Study Reveals