While we try to keep things accurate, this content is part of an ongoing experiment and may not always be reliable.
Please double-check important details — we’re not responsible for how the information is used.
Alternative Fuels
Breaking Down Barriers: Researchers Develop Mercury-Free Method for Isolating Lithium-6
Lithium-6 is essential for producing nuclear fusion fuel, but isolating it from the much more common isotope, lithium-7, usually requires liquid mercury, which is extremely toxic. Now, researchers have developed a mercury-free method to isolate lithium-6 that is as effective as the conventional method.
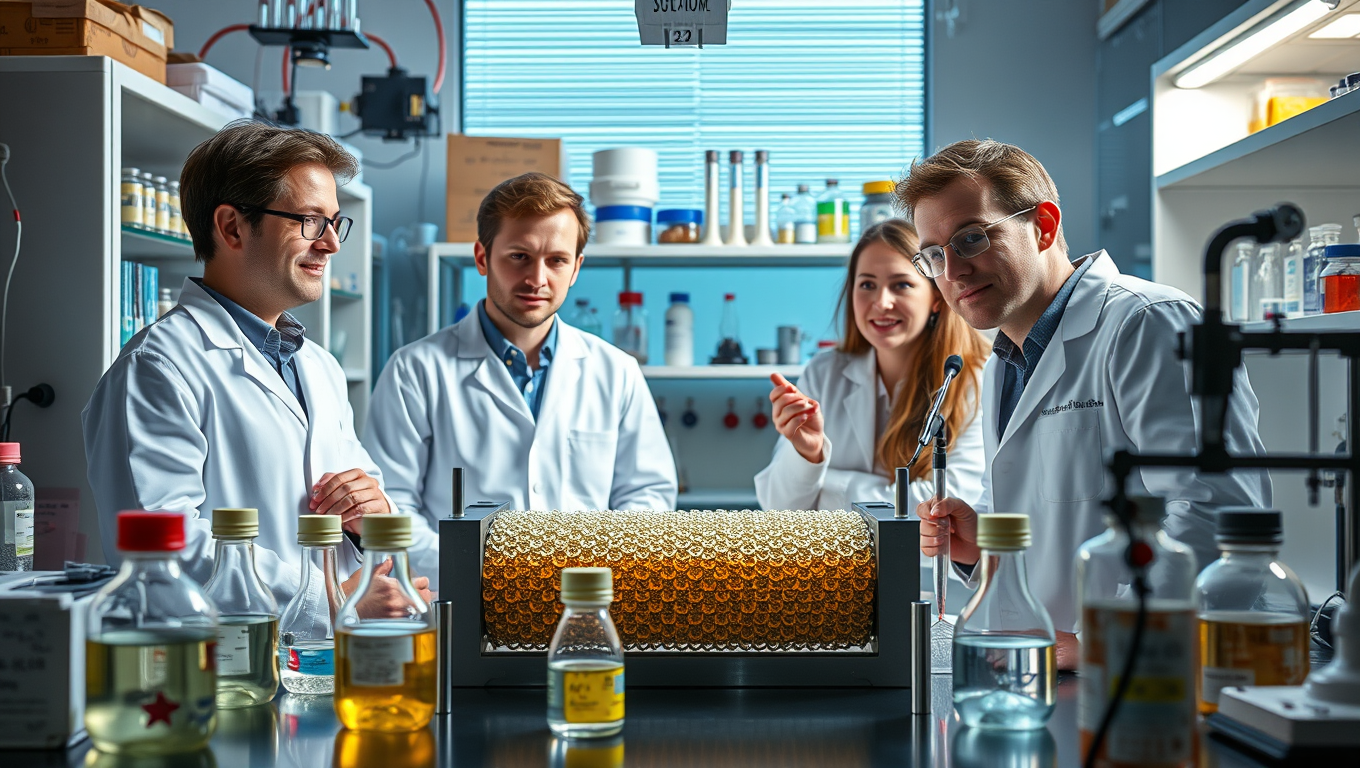
Alternative Fuels
Breaking Ground in Green Energy: An Iron Oxide Catalyst for Efficient Hydrogen Production
As the world shifts toward sustainable energy sources, ‘green hydrogen’ – hydrogen produced without emitting carbon – has emerged as a leading candidate for clean power. Scientists have now developed a new iron-based catalyst that more than doubles the conversion efficiency of thermochemical green hydrogen production.
Alternative Fuels
EV Battery Recycling Key to Future Lithium Supplies
Lightweight, powerful lithium-ion batteries are crucial for the transition to electric vehicles, and global demand for lithium is set to grow rapidly over the next 25 years. A new analysis looks at how new mining operations and battery recycling could meet that demand. Recycling could play a big role in easing supply constraints, the researchers found.
Alternative Fuels
Unveiling Electron Secrets: A Groundbreaking Experiment on the Bound Electron g-Factor in Lithium-Like Tin
Researchers present new experimental and theoretical results for the bound electron g-factor in lithium-like tin which has a much higher nuclear charge than any previous measurement. The experimental accuracy reached a level of 0.5 parts per billion. Using an enhanced interelectronic QED method, the theoretical prediction for the g-factor reached a precision of 6 parts per billion.
-
Detectors4 months ago
A New Horizon for Vision: How Gold Nanoparticles May Restore People’s Sight
-
Earth & Climate5 months ago
Retiring Abroad Can Be Lonely Business
-
Cancer5 months ago
Revolutionizing Quantum Communication: Direct Connections Between Multiple Processors
-
Agriculture and Food5 months ago
“A Sustainable Solution: Researchers Create Hybrid Cheese with 25% Pea Protein”
-
Diseases and Conditions5 months ago
Reducing Falls Among Elderly Women with Polypharmacy through Exercise Intervention
-
Chemistry5 months ago
“Unveiling Hidden Patterns: A New Twist on Interference Phenomena”
-
Albert Einstein5 months ago
Harnessing Water Waves: A Breakthrough in Controlling Floating Objects
-
Earth & Climate5 months ago
Household Electricity Three Times More Expensive Than Upcoming ‘Eco-Friendly’ Aviation E-Fuels, Study Reveals