While we try to keep things accurate, this content is part of an ongoing experiment and may not always be reliable.
Please double-check important details — we’re not responsible for how the information is used.
3-D Printing
“Printing the Future: Soft Artificial Muscles with Real Muscle-Like Properties”
Researchers are working on artificial muscles that can keep up with the real thing. They have now developed a method of producing the soft and elastic, yet powerful structures using 3D printing. One day, these could be used in medicine or robotics — and anywhere else where things need to move at the touch of a button.
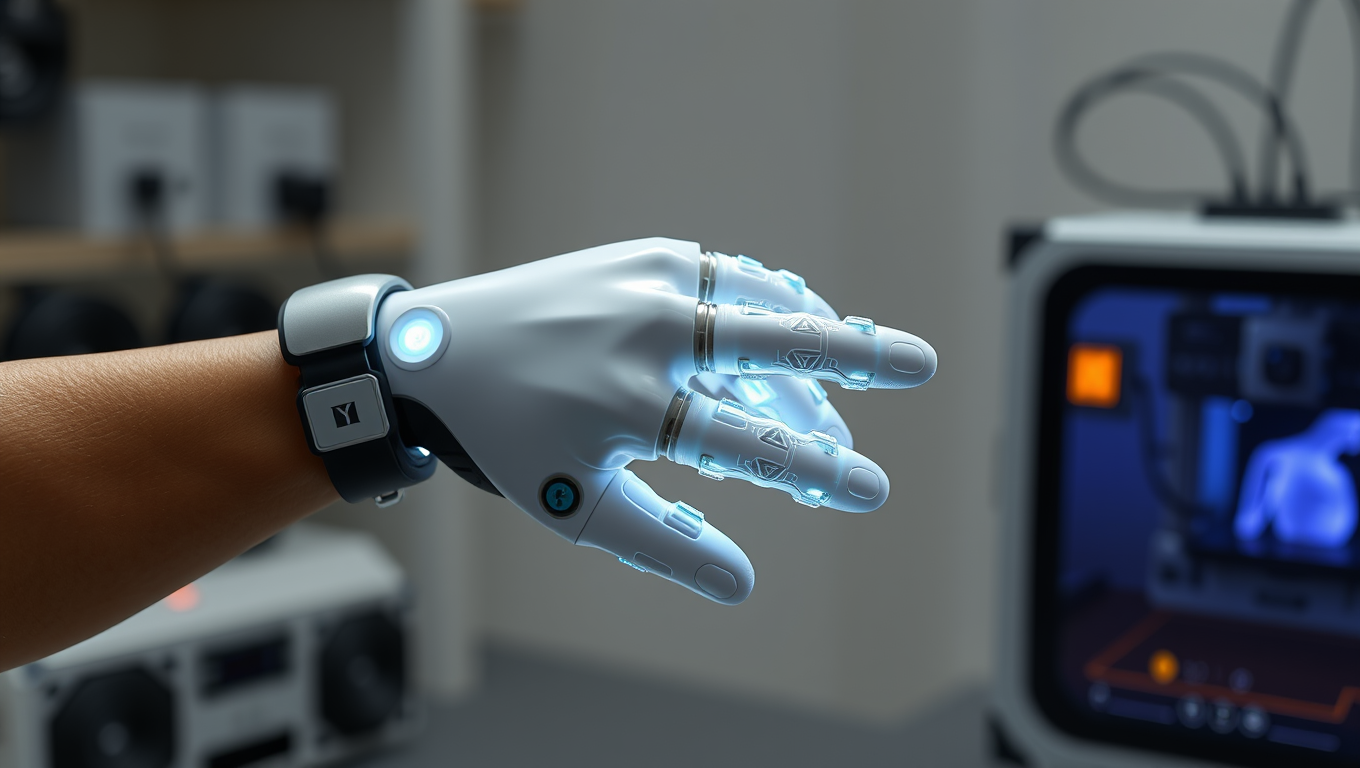
3-D Printing
Breaking New Ground in Smart Wearables: 3-D Printing Technology Boosts Comfort, Durability
Imagine a T-shirt that could monitor your heart rate or blood pressure. Or a pair of socks that could provide feedback on your running stride. It may be closer than you think, with new research demonstrating a particular 3-D ink printing method for so-called smart fabrics that continue to perform well after repeated washings and abrasion tests.
3-D Printing
Revolutionizing Metal 3D Printing with AI-Powered Precision and Efficiency
Researchers are leveraging machine learning to improve additive manufacturing, also commonly known as 3D printing. The team introduces a new framework they’ve dubbed the Accurate Inverse process optimization framework in laser Directed Energy Deposition (AIDED). The new AIDED framework optimizes laser 3D printing to enhance the accuracy and robustness of the finished product. This advancement aims to produce higher quality metal parts for industries, such as aerospace, automotive, nuclear and health care, by predicting how the metal will melt and solidify to find optimal printing conditions.
3-D Printing
A Nature-Inspired 3D Printing Revolution: Speeding Past Bamboo with ‘Growth Printing’
Researchers created ‘growth printing,’ which mimics tree trunks’ outward expansion to print polymer parts quickly and efficiently without the molds and expensive equipment typically associated with 3D printing.
-
Detectors3 months ago
A New Horizon for Vision: How Gold Nanoparticles May Restore People’s Sight
-
Earth & Climate4 months ago
Retiring Abroad Can Be Lonely Business
-
Cancer4 months ago
Revolutionizing Quantum Communication: Direct Connections Between Multiple Processors
-
Agriculture and Food4 months ago
“A Sustainable Solution: Researchers Create Hybrid Cheese with 25% Pea Protein”
-
Diseases and Conditions4 months ago
Reducing Falls Among Elderly Women with Polypharmacy through Exercise Intervention
-
Chemistry4 months ago
“Unveiling Hidden Patterns: A New Twist on Interference Phenomena”
-
Albert Einstein4 months ago
Harnessing Water Waves: A Breakthrough in Controlling Floating Objects
-
Earth & Climate4 months ago
Household Electricity Three Times More Expensive Than Upcoming ‘Eco-Friendly’ Aviation E-Fuels, Study Reveals